Maximizing Efficiency with Automotive Moulds in Metal Fabrication
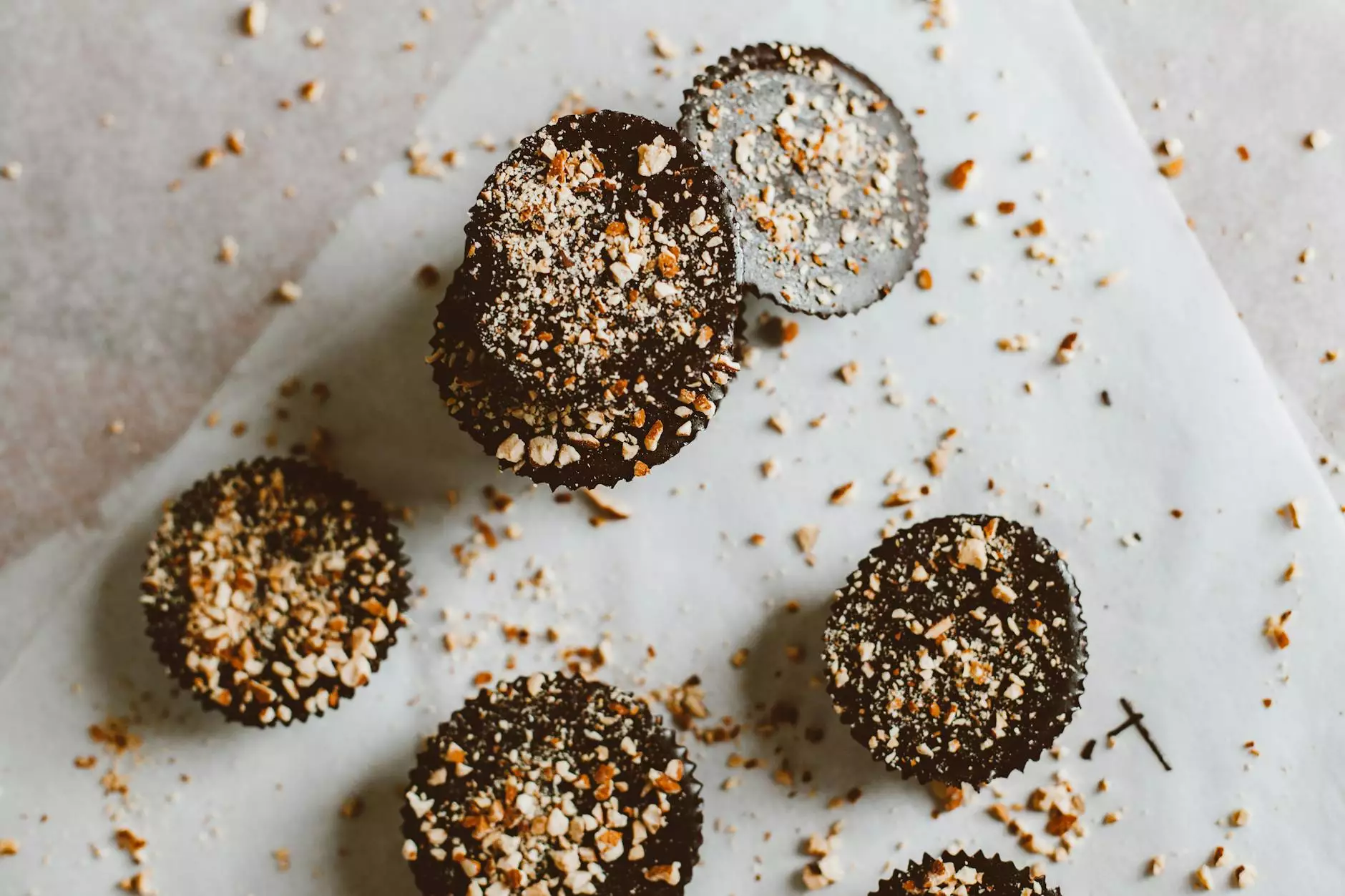
In today's rapidly evolving automotive industry, the demand for high-quality components has never been greater. Automotive mould technologies play a crucial role in satisfying this demand by ensuring precision and consistency in manufacturing processes. This article delves into the significance of automotive moulds, particularly in the realm of metal fabrication, and explores how they are reshaping the landscape of automotive production.
Understanding Automotive Mould Technology
Automotive moulds are custom-designed tools used to shape various metal and plastic parts for vehicles. They facilitate the creation of intricate designs with high precision, making them indispensable in the automotive manufacturing sector. The utilisation of advanced moulding technologies leads to improved product quality and reduced production times.
The Importance of Quality in Automotive Moulds
The effectiveness of an automotive mould directly correlates with the quality of the end product. High-quality moulds are designed to withstand significant pressure and heat, ensuring that they maintain their integrity throughout the production cycle. Some critical factors that contribute to the quality of automotive moulds include:
- Material Selection: The type of materials used in mould fabrication plays a vital role in determining the lifespan and durability of the mould.
- Precision Engineering: Automotive moulds must be engineered with extreme precision to ensure that the parts produced meet stringent quality standards.
- Surface Finish: A well-finished mould reduces friction and the likelihood of defects, enhancing the overall quality of the components produced.
Benefits of Using Automotive Moulds in Metal Fabrication
The integration of automotive mould technologies in metal fabrication processes offers a myriad of benefits that streamline production and enhance product quality. Here are some of the key advantages:
1. Increased Efficiency
One of the most significant advantages of employing automotive moulds is the substantial increase in production efficiency. By allowing for rapid and repetitive manufacturing, moulds reduce the time and effort required to produce complex automotive parts. This not only accelerates production cycles but also leads to a more streamlined workflow.
2. Cost Reduction
Although the initial investment in high-quality automotive moulds can be considerable, the long-term savings are undeniable. By minimizing waste and ensuring that parts are produced accurately, businesses can significantly reduce material costs. Additionally, with enhanced efficiency, labor costs also decrease, leading to a notable reduction in overall production expenses.
3. Enhanced Product Quality
With the implementation of precise automotive moulds, companies can achieve superior product quality. Moulds allow for consistent manufacturing, ensuring that each part meets high quality standards. This consistency results in fewer defects, less rework, and ultimately, greater customer satisfaction.
4. Flexibility in Design
Modern automotive moulds are capable of accommodating various designs, enabling manufacturers to innovate continuously. Advances in technology have made it possible to manufacture complex shapes and features that were once deemed impossible. This flexibility facilitates creative design solutions, allowing manufacturers to meet changing consumer demands quickly.
5. Sustainability
With growing concerns about environmental sustainability in manufacturing, the use of automotive moulds contributes positively. The efficient use of materials and reduction of waste through precise moulding processes help manufacturers align with eco-friendly practices. Additionally, the longevity of high-quality moulds means less frequent replacements, further supporting sustainable manufacturing efforts.
Key Considerations When Choosing Automotive Moulds
Choosing the right automotive mould for your manufacturing needs involves several considerations. To ensure a successful and efficient metal fabrication process, keep the following factors in mind:
- Expertise of the Manufacturer: Partnering with a reputable mould manufacturer like DeepMould.net ensures access to high-quality products and services.
- Customizability: Opt for moulds that can be tailored to meet your specific production requirements.
- Technology Integration: Look for manufacturers that incorporate the latest technological advances in their mould design and production processes.
- Cost vs Quality: While price is an important factor, prioritize quality to avoid long-term costs associated with poor-quality moulds.
The Future of Automotive Moulds in the Metal Fabrication Industry
The future of automotive moulds is bright, with ongoing advancements in technology and materials science. The rise of additive manufacturing and 3D printing is likely to transform traditional mould-making processes, allowing for even more intricate designs and faster prototyping. Additionally, the integration of smart technologies and IoT solutions into mould manufacturing could lead to enhanced monitoring and maintenance capabilities, further boosting efficiency.
Conclusion
As the automotive industry continues to advance, the role of automotive moulds in metal fabrication becomes increasingly vital. By investing in high-quality moulds, manufacturers can enhance production efficiency, reduce costs, and improve product quality. The shift towards sustainability and innovation in this field will ensure that automotive moulds remain a central component of successful manufacturing practices.
For businesses looking to leverage the benefits of automotive mould technologies, partnering with experienced manufacturers like DeepMould.net can provide the necessary expertise and resources. Embrace the future of automotive manufacturing by adopting advanced mould technologies and witness significant improvements in your production capabilities.