Understanding Plastic Molding Factories: Innovation and Impact
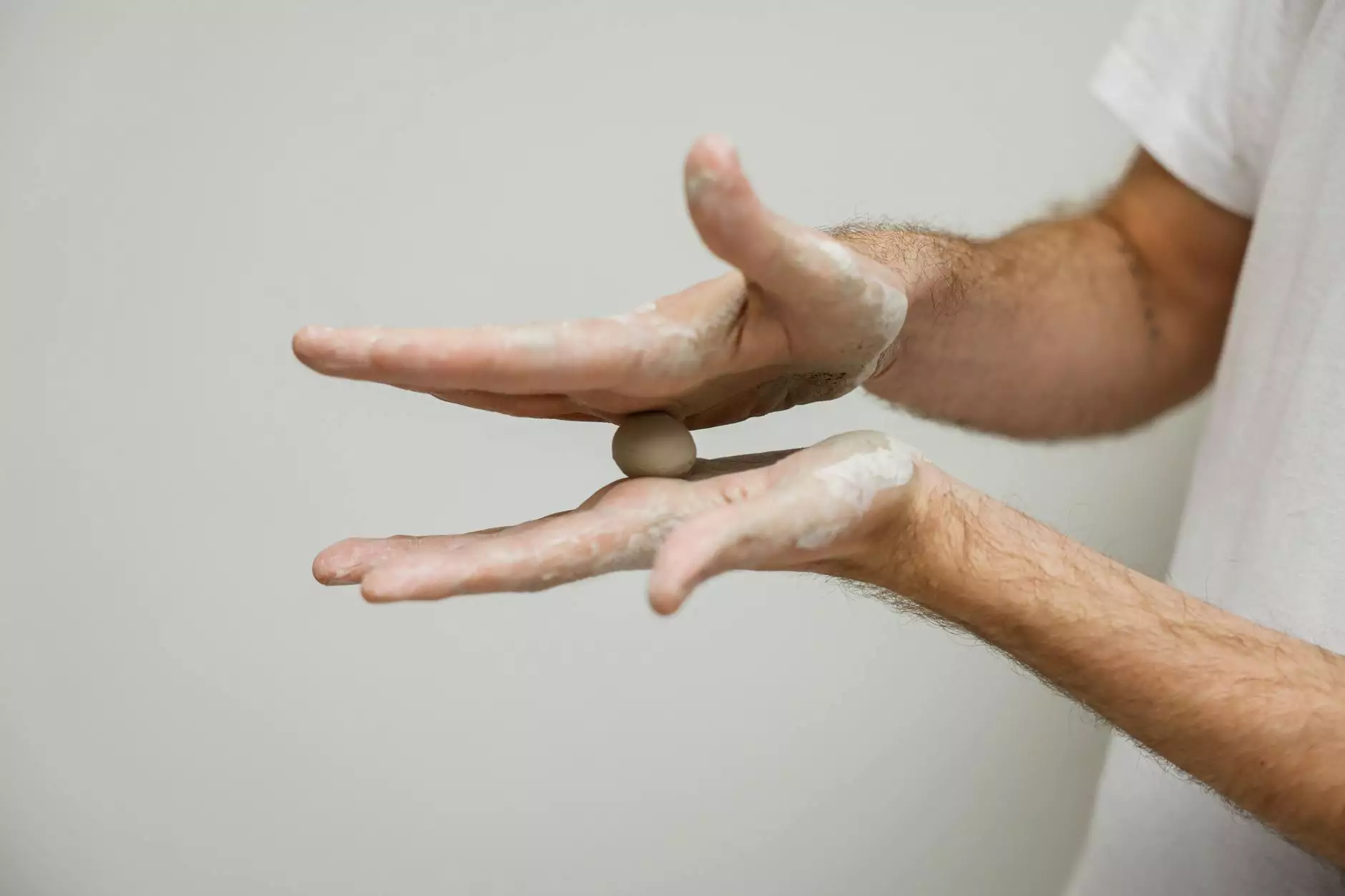
In today’s fast-paced world, industries are always on the lookout for efficient manufacturing processes that can enhance product quality while reducing costs. Among the various manufacturing techniques, plastic molding factory operations stand out as a crucial method in producing a wide array of products, from consumer goods to complex automotive components. In this article, we delve into the intricacies of plastic molding factories, examining their processes, benefits, challenges, and future prospects.
What is Plastic Molding?
Plastic molding is a manufacturing process used to create objects by shaping liquid plastic into a mold. This technique is favored for its versatility and efficiency in producing high volumes of plastic parts with precision. There are several types of plastic molding techniques, including:
- Injection Molding - A process where molten plastic is injected into a mold to form parts.
- Blow Molding - Used to create hollow plastic objects, such as bottles.
- Rotational Molding - Involves rotating a mold filled with plastic to evenly coat the interior surface.
- Thermoforming - A method of heating a plastic sheet and forming it over a mold.
The Role of Plastic Molding Factories in Modern Manufacturing
Plastic molding factories serve as the backbone of numerous industries, providing essential support and materials for a variety of sectors. Here are some major industries that benefit from the capabilities of plastic molding:
1. Automotive Industry
In the automotive industry, weight reduction is crucial for enhancing fuel efficiency. Plastic molding allows manufacturers to create lightweight parts that do not compromise on strength or durability. Components such as dashboards, interior panels, and even exterior fixtures are commonly produced through plastic molding factories.
2. Consumer Goods
The consumer goods market relies heavily on plastic molding to supply everything from household items to electronic casing. The efficiency of the process means that manufacturers can produce large quantities with consistent quality, making it ideal for mass production.
3. Medical Devices
Plastic molding is critical in the healthcare sector, where precision and sterility are paramount. Many medical devices, including syringes, breathing devices, and surgical tools, are manufactured using advanced plastic molding techniques to ensure the highest standards of quality and safety.
Benefits of Using Plastic Molding Factories
The decision to utilize a plastic molding factory comes with numerous advantages:
- Cost-Effectiveness: The mass production capabilities of plastic molding result in lower per-unit costs, making it a financially viable option for large-scale operations.
- Design Flexibility: Plastics can be molded into complex shapes that would be difficult or impossible to achieve with other materials, allowing for innovative product designs.
- Speed of Production: Plastic molding processes can be highly automated, leading to fast production cycles and quick turnaround times.
- Material Variety: A wide range of plastic materials can be used, each offering unique properties to suit different applications.
The Process of Plastic Molding
Understanding the plastic molding process is essential for appreciating how a plastic molding factory operates. The process typically involves the following stages:
1. Material Selection
The first step is choosing the right type of plastic based on the desired characteristics and application of the product. Common materials include:
- Polyethylene (PE)
- Polypropylene (PP)
- Polyvinyl Chloride (PVC)
- Polycarbonate (PC)
2. Melting the Plastic
The selected plastic is then heated until it reaches a molten state. This is a critical stage, as different plastics have varying melting points, and maintaining the correct temperature is essential for effective molding.
3. Injection and Molding
In the injection molding phase, the liquid plastic is injected into a pre-designed mold. The mold is kept under pressure to ensure that the plastic takes its shape accurately. After cooling, the mold is opened, and the formed part is ejected.
4. Finishing
Once the parts are ejected, they may undergo finishing processes such as trimming, painting, or assembly to meet design specifications before they are shipped out.
Challenges Faced by Plastic Molding Factories
While plastic molding factories enjoy many advantages, they also face several challenges, including:
- Environmental Concerns: The use of plastics raises sustainability issues. Factories are under pressure to adopt environmentally friendlier practices and materials.
- Quality Control: Consistent quality in mass production is vital. Any defects can lead to significant losses, hence the need for robust quality assurance practices.
- Market Competition: With an increasing number of players in the industry, factories must innovate and improve efficiencies to remain competitive.
The Future of Plastic Molding Factories
The future of plastic molding factories is promising, driven by technological advancements and an increasing focus on sustainability. Some trends shaping the future include:
1. Customization and On-Demand Production
The demand for customized products is rising, and advancements in molding technologies will allow factories to cater to these needs efficiently.
2. Sustainable Practices
Recycled plastics and biodegradable materials are making their way into production processes, reducing the environmental impact of plastic molding.
3. Automation and Smart Manufacturing
The incorporation of robotics and IoT in factories enhances operational efficiency, reduces errors, and minimizes human intervention in repetitive tasks.
Conclusion
In summary, plastic molding factories are at the forefront of modern manufacturing, playing an essential role in various industries. With their capacity for mass production, versatility in design, and cost-effectiveness, they continue to evolve with technology and market demands. As the industry addresses challenges and embraces sustainability, the future holds exciting opportunities for innovation and growth.
For more information on plastic molding and how it can benefit your business, visit deepmould.net. This resource is dedicated to providing insights, services, and latest trends in the world of plastic molding and manufacturing.